
ITALIAN INDUSTRIAL YACHT DESIGN
La creatività in ogni scatto
Concrete Tender 45' photos
https://industrialyachtdes.wixsite.com/italianindustrialy-1/post/concrete-tender-45-photos

PRODUCT, YACHT DESIGN
Visita il Design
Un buon servizio fotografico non dovrebbe essere troppo costoso. Per questo Italian Industrial Yacht Design offre i propri servizi a tariffe accessibili per venire incontro alle tue esigenze. Contattalo/a se desideri prenotare il servizio e provare qualcosa di diverso dal solito servizio fotografico.

SERVIZI DI PROGETTAZIONE
Scarica UN ANALISI DELLA CONCORRENZA
Un esempio di come investigare una tecnologia usata nella qualità del Design Anno 2002, esame di Storia del Design
Andrea Buffa
I ROTOPRODOTTI
VERSATILI
ECONOMICI
ROMA 2002
BIBBLIOGRAFIA
Bibbliografia
“Rotational Molding - Design, Materials, Tooling & Processing” By Glenn L. Beall, 1998
Rotational Moulding of Plastics, Second Edition By R. J. Crawford, 1996
Thermoplastic Foams *Schiume termoplastiche* Di James L. Throne, 1996
Rotational Molding: A Practical Guide
By Paul Nugent, 2001
WEB
Renato De Fusco “Storia de Design”
PREFAZIONE
La versatilità del rotazionale genera molto interesse ed entusiasmo da parte di progettisti e trasformatori, con un conseguente desiderio di sperimentazione. Nel passaggio dall’idea al prodotto, tuttavia, i risultati pur essendo scontati per chi conosce già la materia, risultano a volte sorprendenti per coloro che vi muovono i primi passi. Come ogni tecnologia, infatti, il rotazionale necessita di alcune conoscenze specifiche affinché progetto e prodotto finito siano corrispondenti all’idea originaria.
INTRODUZIONE
Lo stampaggio rotazionale è una tecnologia che utilizza stampi cavi composti dalla sola parte esterna della figura (matrice) e privi della parte interna (punzone). La distribuzione del polimero sulla superficie dello stampo è regolata dalla conduzione del calore necessario per fondere il materiale e dal tempo di contatto delle singole particelle con le pareti dello stampo: si può dire, quindi, che durante la fase di permanenza nel forno, mentre lo stampo ruota, il polimero tocca continuamente le pareti interne dello stesso, si scalda fino a fondere e a questo punto aderisce allo stampo. Ne deriva uno spessore pressoché uniforme, regolato princi-palmente dalla velocità di conduzione del calore attraverso la parete dello stampo e, in secondo luogo, dal tempo di contatto della particella di polimero con la parete calda della matrice.
La costanza dello spessore, decisamente superiore a quella di altre tecnologie quali il soffiaggio e la termo-formatura, non sarà mai comunque assoluta: gli stampi, infatti, non sono perfettamente isotermi e spesso riproducono forme molto complesse, impedendo alla polvere di polimero di avere con tutti i punti dello stampo un identico tempo di contatto.
Tutto ciò può dare luogo a lievi differenze di spessore da punto a punto e a piccole regioni circoscritte, che chiameremo “punti singolari”, dove lo spessore può essere anche significativamente diverso dallo spessore medio del manufatto. Costituiscono, ad esempio, punti singolari le zone corrispondenti alle flange di giun-zione dello stampo, la sommità di una nervatura, gli spigoli vivi, gli sfiati, i kiss-off, etc. Poiché durante lo stampaggio rotazionale, lo stampo vincola il pezzo solo dal lato esterno, la diminuzione di volume che si ha con la solidificazione porta a ritiri che si distribuiscono nelle tre direzioni in funzione anche dei vincoli. Un manufatto molto vincolato, per la presenza di inserti metallici o nervature, o altro, mostrerà ritiri infe-riori alla media nella direzione del vincolo e superiori alla media nelle direzioni in cui il ritiro può avvenire liberamente.
Anche nella fase di raffreddamento è estremamente importante che la temperatura dello stampo sia la più uniforme possibile. Nei punti più esposti al fluido refrigerante, infatti, il raffreddamento e la solidificazione avvengono prima, anticipando il distacco del manufatto dallo stampo rispetto ad altri punti e creano tensioni che potrebbero portare, se elevate, a deformazioni permanenti del pezzo.
Poiché nello stampaggio rotazionale il polimero ricopia la forma interna dello stampo, è possibile, in linea teorica, conferire al prodotto qualunque aspetto superficiale si desideri: sarà sufficiente trattare in modo op-portuno la superficie dello stampo per conferirle l’aspetto desiderato e, durante lo stampaggio, il polimero non farà altro che riprodurre la finitura della matrice.
La capacità di riprodurre i dettagli è influenzata dalla viscosità del polimero allo stato fuso (melt flow-index); ne consegue che quando è necessaria una finitura accurata è estremamente importante tenere conto delle proprietà del polimero da utilizzare. È chiaro che, poiché il polimero copia fedelmente la matrice, eventuali imperfezioni dello stampo (rigature, giunzioni mal eseguite, porosità, etc.) verranno direttamente riprodotte nel pezzo stampato. È quindi di vitale importanza curare le finiture degli stampi in funzione della precisione desiderata per i vari manufatti.
La realizzazione di un prodotto di qualità richiede un’attenzione particolare fin dalle fasi iniziali della pro-gettazione: l’attenzione ai dettagli già in sede di concezione dell’articolo, consente di eliminare alcuni incon-venienti: si possono, ad esempio, ridurre le deformazioni e le distorsioni inserendo nervature nelle superfici piane di grandi dimensioni ed evitando gli spigoli vivi e i vincoli più severi.
In fase di costruzione dello stampo sarà importante anche ridurre al minimo la disuniformità di riscalda-mento: uno stampo in lamiera d’acciaio, può costare meno rispetto a uno stampo in alluminio, ma avrà riscaldamenti meno uniformi, e genererà variabilità di spessore più marcate con raffreddamenti più violenti e maggiori distorsioni e deformazioni. Anche il ciclo di stampaggio ha una grande influenza sul risultato finale: un ciclo lento favorisce un riscaldamento e un raffreddamento uniformi, con conseguente migliore qualità del prodotto finito, ma con costi di produzione più elevati.
Da ciò si evince che lo stampaggio rotazionale è una tecnologia flessibile che permette di ottenere, con investimenti modesti, manufatti dove non siano richieste tolleranze spinte. Tolleranze più ristrette possono invece essere raggiunte con maggiori investimenti nella progettazione, nella realizzazione di modelli e stampi, nella cura delle attrezzature di stampaggio e dei cicli di produzione.
SPESSORE
Nello stampaggio rotazionale in polietilene gli spessori delle pareti vanno, normalmente, da un minimo di circa 1 mm a un massimo di 15 mm. Esistono comunque casi di manufatti di grandi dimensioni con spes-sori anche maggiori. Il modo più appropriato per definire lo spessore di un articolo stampato in rotazionale è quello di indicare lo spessore nominale e quello minimo ammissibile in qualunque punto.
La tolleranza sullo spessore è legata alla forma e alla dimensione del manufatto nonché all’accuratezza dello stampaggio.
ASPETTO SUPERFICIALE
Concorrono all’ottenimento di un buon aspetto superficiale molteplici fattori. Come indicazione generale
si può affermare che la superficie esterna del pezzo non potrà essere migliore di quella della cavità interna
dello stampo.
Finitura (Texture)
Svariate sono le finiture superficiali ottenibili per stampaggio rotazionale: lucida, sabbiata, pallinata, etc.
In generale per poter definire la superficie desiderata conviene riferirsi a campioni stampati preesistenti.
COLORE
Esistono sostanzialmente due sistemi di pigmentazione del materiale da stampaggio rotazionale: 1) a secco, dove il pigmento viene miscelato al polietilene in polvere; 2) per estrusione, dove pigmento e resina vengono mescolati allo stato fuso e successivamente granulati e polverizzati.
La pigmentazione a secco può portare a colorazione non uniforme e porosità superficiali; peraltro, essa presenta un costo più contenuto e un’ampia gamma di colorazioni ottenibili (anche per piccoli lotti).
La pigmentazione per estrusione presenta una colorazione più omogenea con una minor porosità superfi-ciale; essa ha però un costo maggiore e una minore versatilità nella gamma dei colori disponibili.
Per la scelta del colore è buona norma definire con il trasformatore l’intervallo di accettabilità sulla base di campioni ottenuti anch’essi per stampaggio rotazionale.
POROSITA’
Le porosità superficiali si possono presentare come cavità di diametro inferiore al millimetro più o meno densamente distribuite. Esse possono avere diverse cause, quali la rugosità superficiale o la porosità dello stampo, l’indice di fluidità (M.F.I.) troppo basso, la cattiva miscelazione del materiale con il pigmento, la presenza di spigoli vivi nel pezzo. Questi difetti possono essere rimossi adottando opportuni accorgimenti progettuali, e impiegando materiali ed attrezzature di migliore qualità (e costi maggiori).
I ROTOPRODOTTI
Nel 1947 si brevettata la tecnologia dello stampaggio rotazionale Questo processo produttivo nasce negli Stati Uniti per i grandi numeri nel settore degli imballaggi e nelle applicazioni industriali
Lo stampaggio a rotazione è un metodo di produzione altamente versatile che aggiunge alle sue illimitate possibilità progettuali anche il beneficio di bassi costi di produzione.
Sommario del processo.
Il processo di stampaggio a rotazione inizia con il piazzamento di uno stampo di buona qualità in una macchina per lo stampaggio dotata di zone di caricamento, riscaldamento e raffreddamento.
possibile collocare nella macchina più di uno stampo allo stesso tempo. Viene quindi introdotta in ogni stampo una quantità predosata di resina di plastica e gli stampi vengono posti all’interno di un forno dove sono ruotati lentamente lungo entrambe l’assi, verticale ed orizzontale. Fondendo, la resina si attacca allo stampo caldo ricoprendone tutta la superficie in maniera uniforme. Lo stampo continua a rotare durante il ciclo di raffreddamento in modo da mantenere uguale la misura dello spessore delle pareti dei pezzi.
Una volta raffreddati, i pezzi vengono rilasciati dallo stampo. La velocità di rotazione ed i tempi di riscaldamento e raffreddamento sono controllati durante tutto il processo.
Materiali che possono essere utilizzitati
La continua ricerca di nuovi materiali e tecnologie amplia ogni anno la gamma di polimeri che possono essere efficacemente utilizzati nello stampaggio rotazionale. Attualmente la maggior parte della produzione viene effettuata con polietilene lineare e reticolato, pvc, polipropilene, poliammide, policarbonato.
Applicazioni dello stampaggio rotazionale
Innumerevoli, e in continua crescita grazie alla maggiore conoscenza di questa tecnologia da parte di progettisti e produttori.
Non esiste settore in cui non trovi applicazione un prodotto stampato in rotazionale. Nelle fotografie qui sotto riportate è esposta una breve rassegna, non certo esaustiva, dei prodotti realizzabili.
Vantaggi di progettazione
Stampi meno costosi, possibilità di produrre in serie limitate, possibilità di realizzare forme molto complesse e di grandi dimensioni.
Produzione di corpi cavi in un solo pezzo senza necessità di saldature. Pezzi privi di tensioni interne. Buona uniformità di spessore dei prodotti.
Possono essere stampati articoli di grosse dimensioni con contorni molto complicati, anche con differenti finiture superficiali (finta pelle, goffrature etc.) e con diversi tipi di inserti costampati.
Offre vantaggi di progettazione non condivisi da altri processi di stampaggio. Se progettate correttamente, diversi pezzi possono essere stampate come unico pezzo, eliminando così alte spese di produzione.
Il processo presenta inoltre un certo numero di punti di forza inerenti alla progettazione, quali la consistenza dello spessore delle pareti dei pezzi e la robustezza dei loro angoli esterni che sono virtualmente esenti da qualsiasi sollecitazione. Nel caso un pezzo richiedesse maggiore robustezza, è anche possibile progettare la creazione di elementi rinforzanti al suo interno.
I progettisti hanno la possibilità di scegliere il materiale che meglio si adatta alle loro applicazioni, (inclusi quei materiali approvati dalla FDA). È inoltre possibile specificare quali additivi usare per rendere il pezzo resistente agli agenti atmosferici, antifiamma o antifulmine.
Inserti, filettature, maniglie, piccole rientranze, superfici piatte o dettagli di superfici possono tutti far parte del progetto. La possibilità di produrre pezzi a pareti multiple che possono essere lasciate vuote o riempite con espanso.
Vantaggi di costo
Quando il costo è un fattore da considerare, lo stampaggio rotazionale è sempre vantaggioso se paragonato ad altri tipi di produzione, i costi di investimento in attrezzature sono decisamente più contenuti. In confronto a stampaggi a iniezione o a soffiature, lo stampaggio a rotazione può facilmente creare piccoli e grandi pezzi con la massima efficienza. L’attrezzatura è meno costosa perché non c’è anima interna da fabbricare. Di conseguenza, nel caso ci siano delle piccole modifiche da apportare, ciò può essere facilmente effettuato sullo stampo esistente.
E siccome i pezzi vengono formati non a pressione, ma a seguito di riscaldamento e rotazione, gli stampi non devono necessariamente essere progettati per resistere alle alte pressioni dello stampaggio ad iniezione.
Le spese di produzione per la conversione dei prodotti sono ugualmente ridotte in quanto materiali spesso più pesanti e costosi sono ora sostituiti da plastiche leggere. Quanto descritto rende lo stampaggio a rotazione efficiente, in termini di costi, sia per la produzione di prototipi unici che per produzioni all’ingrosso.
Stato della tecnica e scenari futuri
L’industria dello stampaggio rotazionale è in continua espansione ed evoluzione.
Le sfide per questo cresente mercato non sono tante e tanti invece sono i risultati, i limiti rimango nella sfida del colore che presenta ancora numerose difficoltà rispetto alle esigenze sempre più crescenti.
Dal 1933, il polietilene diviene di uso frequentissimo nell’industria.
L’ unico problema connesso con polietilene, è che rifiuta i metodi usuali di decorazione. Per i 50 anni scorsi, il mezzo più comune di decorazione del polietilene è stato schermature di seta, pitture sovrastanti, attaccature sulle etichette di carta o trasferimento di etichette chimiche. Ma questi metodi di decorazione infine vengono a meno una volta esposti agli agenti esterni.
Il polietilene, per la relativa natura, non si presta ad alcun metodo di adesione della ver-nice, e non essendo poroso, è resistente all’attacco dai solventi, utili nella formulazione della vernice ed ha una struttura chimica non polare.
Ma già si avvia la terza espansione.
Macchine sempre più di precisione e di controllo, ed una serie crescente di materiali appropriati espandono il potenziale del rotazionale e sempre più aziende si convertono in questa tecnologia, la domanda incentiva e velocizza la ricerca. Dall’america si intravedono materiali di nuova concezione, polimeri liquidi.
Polietilene, nailon, macchinari sempre più versatili, forni in cui si possono variare le temperature secondo i punti d’interesse nella medesima lavorazione.
Fogli metallici plasmabili per nuovi stampi versatili, Singola o duplice pareti, Studi del Caso del Disegno, Controllo del processo Rotazionale, Schiume termoplastiche con aspetti tecnici pratici a diverse densità, Potenziali proprietà di Isolamento, Mitigazione d’Impatto, Galleggiabilità, Polimeri, Schiume Polimeriche, Superfici finto- Pelle.
L’innovazione dei materiali propone scenari davvero ragguardevoli, e sicuramente inaspettati.
Versalità della tecnologia e design appropriato e variegato. Insomma lo scenario è imprevedibile visto che impiega già molteplici se non universali campi.
(mobili e arredamento, nautica, sicurezza stradale, attrezzature industriali, automotive, contenitori, ecologia , giardinaggio, imballaggio, tempo libero, giochi).
STAMPAGGIO ROTAZIONALE
Creatività e studi su nuovi prodotti aprono vie diverse per questa tecnologia che risulta conveniente anche per produzioni di bassi quantitativi. Quest’ultimo aspetto è di primaria importanza vista la riduzione dei cicli di vita dei prodotti che impongono costanti novità. Lo stampaggio rotazionale è concepito per realizzare corpi cavi, a partire da medie dimensioni, con materiali termoplastici in polvere. Lo stampo femmina, contenente il materiale, è cotto in forno e ruota su due assi perpendicolari fondendo omogeneamente la plastica sulle pareti.
Non esiste un settore in cui non sia interessante un prodotto stampato in rotazionale.
Si ottengono stampati senza saldatura con spessori regolari ed omogenei. I prodotti possono essere anche di grandi dimensioni, fino a 2000 litri di volume, con contorni molto elaborati e complessi, con o senza inserti annegati, con la possibilità di ottenere finiture superficiali sabbiate, goffrate o in finta pelle. Gli articoli realizzati sono resistenti alle basse temperature e agli agenti chimici, e possono essere a doppia parete, con possibilità di schiumature interne per isolare o rinforzare il manufatto.
Gli stampi vengono progettati in azienda e seguiti nell’esecuzione interna o esterna. Possono essere in lamiera per le forme più semplici e in fusione di alluminio per le forme più complesse. I costi di attrezzatura sono comunque molto più contenuti rispetto ad altre tecnologie.
COME FUNZIONA LO STAMPAGGIO ROATZIONALE
FASE 1
Si carica uno stampo cavo con materia plastica in polvere o liquida.
FASE 2
Lo stampo chiuso viene fatto ruotare in un ambiente riscaldato in modo che la materia plastica possa fondere e depositarsi uniformemente su tutte le pareti
FASE 3
Lo stampo viene raffreddato mantenendolo in rotazione in modo che la materia plastica solidifichi conservando la forma interna dello stampo
FASE 4
Lo stampo viene aperto per estrarre il
pezzo.
Può ripartire un nuovo ciclo
Una Storia tutta Italiana
SERRALUNGA
http://www.serralunga.com/ PIETRO SERRALUNGA srl Via Serralunga,9 13900 BIELLA-ITALY
e-mail serralunga1825@biella.alpcom.it Tel. +39 015 2435711 Fax. +39 015 31081
L’azienda è nata nel 1825, si sviluppa su 27.000 m2 ed è situata in Biella a circa 80 km da Milano (ITALY).
La proprietà è attivamente presente da cinque generazioni in azienda.
L’affidabilità, la qualità, la serietà sono garantite da decenni d’esperienza e di tradizione.
Disponiamo di macchinario per lo stampaggio delle materie plastiche e per la trasformazione di altre materie prime.
Esportiamo il 50% della nostra produzione in 42 paesi.
I settori in cui operiamo prevalentemente sono:
Accessori per l’industria tessile della filatura
Fioriere in plastica realizzate nel tipico stile italiano
Progettazione, realizzazione stampi e stampaggio conto terzi.
SERRALUNGA, è un’azienda biellese con una tradizione di più di 170 anni. Nata prima della rivoluzione industriale, nel suo cammino ha cambiato tipologie di materiali, diventando oggi leader nella produzione di fioriere in plastica ITALIAN STYLE, si sviluppa su 12.000 mq e occupa 60 persone. Il concept dell’azienda è quello di rivisitare i prodotti realizzati con materiali tradizionali e ponendo una grande attenzione all’evoluzione dei polimeri, applica le tecnologie più evolute della plastica verso nuovi oggetti, tenendo invariato l’uso e la funzionalità degli stessi. Rispetto ai tradizionali vasi economici in polimero la SERRALUNGA pone la massima attenzione alla creatività ed al gusto dell’innovazione, non banale, e alla massima cura nei dettagli sia di tipo estetico che funzionale. Non ultimo il vaso viene interpretato con un pò della tradizionale ironia italiana.
La ricerca progettuale e produttiva in Italia ha ancora da giocare molte carte, non tutte ancora scoperte: meglio e probabilmente da riscoprire. Piccole conferme di una non sopita inventiva italiana affiorano sparse un po’ ovunque anche nel comprensorio storicamente tessile del Biellese famoso per affermate o più recenti firme dell’abbigliamento: Loro Piana, Ermenegildo Zegna, Fila, solo per ricordarne alcune. Serralunga 1825 deve il suo nome all’anno in cui fu fondata come selleria a Biella, nella via che porta lo stesso nome (presente alle grandi Esposizioni nazionali degli albori del Novecento, famiglia che poi annovera uomini politici e senatori del Regno). Riconvertita alla produzione di componenti in plastica per macchinari tessili, ricerca ora la sua seconda affermazione proprio nella plastica, adottando la tecnologia dello stampaggio rotazionale per dar vita a quei particolari oggetti che sono le fioriere e in genere i vasi da giardino. Dalla pedissequa e ben riuscita imitazione dei modelli classici (fino alle vette del cotto “stile Rotazionale”, con l’artificio di una finta muffa che infiora i bassorilievi) ma anche in nuove forme e grandi formati, resi entrambi possibili dalla nuova tecnologia.
Questo processo produttivo nasce negli Stati Uniti per i grandi numeri nel settore degli imballaggi e nelle applicazioni industriali. Solo pochi anni fa l’industriale Marco Serralunga con l’architetto Luisa Bocchietto, ne hanno intravisto l’applicazione per sviluppare una produzione di vasi e fioriere, contraddistinta da forme innovative, un massiccio ricorso al fuori scala e a colorazioni vivaci.
Il debutto nella “high society” dei design è arrivato nel fatidico 2000 con l’allestimento di una stanza in Triennale per la mostra Essere/Benessere, con una successiva “dichiarazione di indipendenza” in occasione del Salone del Mobile 2001.
Per costruire il paesaggio del nuovo catalogo sono state fatte scelte mirate, convocando inizialmente designer italiani: Paolo Rizzatto, autore con New Pot di una rilettura fuori scala del semplice vaso in cotto a tronco di cono, poi sviluppato, sia nelle dimensione che nella superficie, con scanalatura dorica nel totemico vaso Eufronio: Alberto Meda, che ha
lavorato sul cerchio e l’ellisse, componendoli nei vasi e sottovasi Disco, Ellisse Volante, In Orbita:
Rodolfo Dordoni, che con Ming ha giocato sulla rastremazione; Lorenzo Clerici
Alba Gallizia, con decorazioni a rilievo e l’introduzione di supporti metallici in Evasol e Evaso 2: Luisa Bocchietto, coordinatrice della collezione, con i più spigolosi Kabin contenitori e vasi tronco-piramidali con piedini. Per poi stuzzicare il genio di Santachiara, che da subito ha rotto gli schemi disegnando un vaso ‘torchon’ da pendio- Santavase- per poi variare sul tema con un vaso pendente da terreno piano, non potendo chiamare che Pisa. La collaborazione si è quindi aperta agli ‘stranieri’: tra gli atri, Ron Arad, il primo a pensare un vaso estensibile, disposto a piacere nello spazio, e che - a tal punto impressionato dagli esiti delle collezioni e dalle possibilità di questa applicazione - ha pensato di portare i propri studenti di design proprio a Biella: in via Serralunga, proprio accanto alla Fondazione Pistoletto. Il vaso “a fisarmonica” di Arad è ancora un prototipo, ma la realizzazione è prossima, anche grazie ai carichi differenziati e alla flessibilità che la tecnica rotazionale consente:
quasi alla ricerca del “punto di rottura”, come in una barocca esecuzione di un Concerto grosso: dove ‘barocco’ è esclusiva connotazione storica e gli strumenti solisti sono i designer che dialogano con gli imprenditori, sostenuti dall’orchestra produttiva e dalle solide basi di un mercato che fa da basso continuo.. Mercato, appunto, perché questi vasi fuori scala, ludiche fioriere, contenitori scalari, si posizionano saggiamente in una fascia media. Cosa catalizza l’interesse dei designer, dei giornalisti, degli storici per questo angolo remoto? Il critico Renato De Fusco ha inserito Serralunga nell’aggiornamento della sua “Storia de Design”, scomodando addirittura il Rinascimento per descrivere questi oggetti “fatti d’aria” e autoportanti, grazie alle esili, differenziate pareti di plastica in spessore di qualche millimetro.
Molto si deve ovviamente allo stampaggio rotazionale, che con l’air moulding costituisce una valida alternativa all’iniezione. Lo stampo è in alluminio quindi molto meno costoso dei tradizionali stampi d’acciaio per
l’iniezione - e consente la realizzazione di pezzi in piccola serie (l’ammortizzamento dello stampo è ovviamente più rapido), anche in grandi dimensioni (si va oltre i due metri). La polvere di polietilene (si utilizzano anche polipropilene, Nylon e PVC in minor misura), in varie colorazioni, viene immessa nello stampo bivalve: per effetto della rotazione e per gravità, aderisce perfettamente alle pareti durante i circa venti minuti di permanenza nel forno (la cottura va dai 18 ai 30 minuti), distribuendosi in spessori calcolati in funzione della tenuta (differente per sedute, vasi, contenitori, ecc). Una volta raffreddato e tolto dallo stampo il pezzo, ancora leggermente caldo e malleabile, viene rifinito (con aria compressa) dal primo intervento della mano artigiana, cui segue, una volta raffreddato, una pulitura delle eventuali sbavature. La tecnica ha ancora dei limiti, nelle colorazioni o nelle finiture, per esempio per quanto riguarda il lucido: permette però diverse soluzioni, sia nel trattamento della superficie (rugosità e crettatura), sia nell’intensità del pigmento).
La sperimentazione sulle caratteristiche strutturali e funzionali sposta però via via questi limiti verso esiti un tempo impensati, ma oggi raggiungibili grazie alla ricerca (è recente l’annuncio della messa a punto nei laboratori del Politecnico di Milano di una nuova plastica, riciclabile al 90% - notizia che rievoca i fasti gloriosi dello scoperte del Nobel Natta), fino allo studio di un vaso ‘interattivo’, capace cioè di comunicare lo stato di salute della pianta tramite il costante monitoraggio delle condizioni del terriccio. Per il momento lo sviluppo del prodotto firmato Serralunga avviene nel circostanziato settore di pertinenza, le “architetture da giardino”, per una precisa scelta strategica e distributiva: ma è lecito chiedersi fino a quando.
SERRALUNGA
Progettazione, realizzazione stampi e stampaggio conto terzi
Disponiamo di presse da 60 ton a 1000 ton e trasformiamo ogni tipo di materiale plastico (polipropilene, poliammide, policarbonato, polietilene, resina acetalica, polisulfoni).
Le nostre macchine sono automatizzate e robotizzate per garantire affidabilità e costi contenuti.
Stampiamo prodotti destinati ad essere impiegati nei settori più disparati:
AUTO, MOTO, ELETTRICITA’, ALIMENTI, ARREDI, GIOCATTOLI.
Disponiamo di presse speciali per la realizzazione di prodotti di media grammatura che richiedono estrazioni lungo l’asse delle colonne senza giunzioni sui lati.
Il nostro ufficio tecnico progetta stampi anche complessi e ne cura la realizzazione. La tecnologia dello stampaggio rotazionale è stata introdotta in azienda a partire dal 1976.
Le dimensioni massime degli articoli stampati possono raggiungere i 2000 LT di volume.
Notevole l’esperienza accumulata nella realizzazione di articoli con contorni molto complessi ed elaborati, a doppia parete, con inserti metallici annegati, con la possibilità di ottenere vari tipi di finiture della superficie (sabbiata, goffrata, finta pelle, pallinata, lucida).
Importante anche l’esperienza nella verniciatura ed assemblaggio degli stampati. Utilizziamo regolarmente vari tipi di materie prime (polietilene lineare, polietilene reticolato, PVC, polipropilene) e la ricerca amplia , di anno in anno, la gamma di polimeri utilizzabili con questo metodo di stampaggio. Stampiamo:
FIORIERE, PROMUOVENDO NUMEROSI NUOVI MODELLI NEL RISPETTO DEL TIPICO DESIGN ITALIANO
CONTENITORI PER IL SETTORE TESSILE E AGRICOLO CONTENITORI PER L’INDUSTRIA DEL GELO SERBATOI PER MOTOVEICOLI
Inoltre produciamo per conto di numerosi clienti articoli specifici che spaziano in vari settori d’impiego (automobilistico, ecologia, alimentare ecc.).
Il nostro ufficio tecnico progetta stampi anche complessi e ne cura la realizzazione.
Una linea di vasi al top. Il design rivoluziona la percezione della fioriera. Il vaso, vissuto fino ad ora come semplice contenitore di piante e fiori, come prodotto generico per il quale non viene data grande importanza alla marca ed all’estetica, diventa protagonista dello scenario domestico. L’idea é la nuova linea di vasi e fioriere per interni ed esterni disegnata da Ron Arad, Luisa Bocchietto, Lorenzo Clerici e Alba Gallizia, Rodolfo Dordoni, Alberto Meda, Karim Rashid, Paolo Rizzatto, Denis Santachiara. Il vaso diventa un vero e proprio complemento d’arredo, che contribuisce a decorare e a personalizzare l’ambiente. Un oggetto di design, che sottolinea l’attenzione per il particolare e si distingue per ricerca estetica, materiali e tecnologia produttiva. Tutti i vasi sono realizzati in materiale plastico per risultare leggeri rispetto ai tradizionali vasi in terracotta e più resistenti agli agenti atmosferici e all’usura del tempo. Il metodo rotazionale, con cui vengono realizzati, consente una notevole versatilità delle forme, raffinata qualità estetica ed alta resa tecnica.
Dal 1825 produciamo accessori per l’industria tessile, allora in cuoio prodotto dalla nostra conceria, dal 1960 in plastica, in gomma, in altri materiali sintetici. Cooperiamo con le principali aziende mondiali produttrici di macchinario per la fornitura. Forniamo i principali gruppi tessili mondiali lanieri e cotonieri.
La decennale presenza commerciale nel mercato tessile mondiale testimonia la nostra affidabilità.
Stampaggio a Iniezione
Disponiamo di presse da 60 ton a 1000 ton e trasformiamo ogni tipo di materiale plastico
(polipropilene, poliammide, policarbonato, polietilene, resina acetalica, polisulfoni). Le nostre macchine sono automatizzate e robotizzate per garantire affidabilità e costi contenuti.
Stampaggio rotazionale
La tecnologia dello stampaggio rotazionale è stata introdotta in azienda a partire dal 1976.
Le dimensioni massime degli articoli stampati possono raggiungere i 2000 LT di volume.
Notevole l’esperienza accumulata nella realizzazione di articoli con contorni molto complessi ed elaborati, a doppia parete, con inserti metallici annegati, con la possibilità di ottenere vari tipi di finiture della superficie (sabbiata, goffrata, finta pelle, pallinata, lucida).
Importante anche l’esperienza nella verniciatura ed assemblaggio degli stampati. Utilizziamo regolarmente vari tipi di materie prime (polietilene lineare, polietilene reticolato, PVC, polipropilene) e la ricerca amplia , di anno in anno, la gamma di polimeri utilizzabili con questo metodo di stampaggio. Stampiamo:
FIORIERE, PROMUOVENDO NUMEROSI NUOVI MODELLI NEL RISPETTO DEL TIPICO DESIGN ITALIANO
CONTENITORI PER IL SETTORE TESSILE E AGRICOLO CONTENITORI PER L’INDUSTRIA DEL GELO SERBATOI PER MOTOVEICOLI
Inoltre produciamo per conto di numerosi clienti articoli specifici che spaziano in vari settori d’impiego (automobilistico, ecologia, alimentare, ecc.).
Il nostro ufficio tecnico progetta stampi anche complessi e ne cura la realizzazione.
Stampiamo prodotti destinati ad essere impiegati nei settori più disparati:
I settori d’applicazione sono molteplici mobili e arredamento, nautica, sicurezza stradale, attrezzature industriali, automotive, contenitori, ecologia , giardinaggio, imballaggio, tempo libero, giochi.
CONTROLLO DI QUALITA’
Il controllo della qualità del prodotto garantisce forniture con caratteristiche qualitative costanti nel tempo. Per raggiungere questo obiettivo Serralunga si è dotata, oltre che di metodologie di lavoro adeguate (quali controlli all’accettazione delle materie prime, e controlli on line durante la produzione), di un laboratorio di controllo qualità efficiente e attrezzato, nel quale vengono utilizzati
-apparecchi per controllo MELT INDEX e grado VICAT,
-forno a muffola per controllo ceneri e prove termiche,
-pendolo per prove d’urto con metodologie Charpy e Izod
-dinamometro per prove meccaniche di trazione, torsione e compressione,
-intaglia provini,
-pesa analitica,
-rilevazione grafica delle analisi eseguite.
SERRALUNGA E’ IN GRADO DI OFFRIRE L’AUTOCERTIFICAZIONE DEI PRODOTTI E DI OFFRIRE FORNITURE IN GARANZIA SPECIALE
Questi i nostri principali prodotti:
Coni e cilindri per roccatura, coni e cilindri forati per tintoria e vaporizzo, tubi per finitore e per banco a fusi, tubetti per filatoio, vasi per filatura e loro accessori, cinghiette e rivestimenti in gomma per stiro, manicotti, lanieres e cannelle per carda, ballons cots e manicotti per finitore, ricambi per open end, cilindri in cartone.
TECNOLOGIE
INGEGNERIZZAZIONE DEI PRODOTTI
Il prodotto vincente è sempre frutto di una precisa analisi progettuale dove know-how, stampi adeguati, tecnologie produttive all’ avanguardia e attenta scelta della materia prima sono gli strumenti per realizzarlo. Una dettagliata analisi di fattibilità, che valuta le tipologie di utilizzo, i requisiti qualitativi essenziali, le caratteristiche estetiche e funzionali, i quantitativi, conduce alla realizzazione del progetto cui, su richiesta, seguirà la realizzazione del primo prototipo in polistirolo, legno, gesso o resina. Appurata l’idoneità del prototipo, vengono individuate le tecnologie produttive adatte per poi passare alla progettazione e realizzazione degli stampi. A questi ultimi viene dedicata particolare attenzione in quanto rappresentano la vera spina dorsale del prodotto finito. La ditta Serralunga realizza, al suo interno o presso officine qualificate, stampi fino a decine di impronte assistendo il cliente dal progetto al prodotto.
VALORI
Operare con assoluta serietà, credere nel lavoro di gruppo e nella competitività, essere orientati al conseguimento dei migliori risultati, perseguire la massima soddisfazione del cliente e investire nella ricerca sono i valori su cui si fonda la cultura aziendale della SERRALUNGA.
La traduzione coerente di questi valori nella pratica lavorativa ha permesso alla azienda di diventare leader nei prodotti di gusto made in Italia.
RICERCA E SVILUPPO
SERRALUNGA opera in un mercato dove il fattore competitività ha come prerogativa ineludibile la capacità di proporre soluzioni che sappiano recepire e soddisfare le esigenze specifiche dei clienti. La strategia dell’Azienda è pertanto quella di essere continuamente all’avanguardia sia sotto l’aspetto tecnologico che innovativo, investendo nella ricerca per conquistare con prodotti di qualità una quota di mercato sempre maggiore e dando vita ad importanti collaborazioni.
LE RISORSE UMANE
La formazione continua del proprio personale rappresentano un contributo importantissimo al miglioramento delle competenze tecniche e professionali dei suoi dipendenti e alla crescita culturale e produttiva dell’intera Azienda.
LOGISTICA
La logistica è parte integrante del business di Serralunga, ed è strutturata in tre aree: Pianificazione, per la gestione degli approvvigionamenti, Customer Service al trade e al consumo e Distribuzione.
Si è organizzata secondo la Supply Chain, presidiando tutta la catena, dalla produzione al consumatore finale: se la soddisfazione, e quindi la fedeltà nel tempo dei clienti sono un fattore critico di successo, la logistica deve rispondere a tutti quei servizi che, ben percepiti, possono dare un valore aggiunto al prodotto.
GLOSSARIO
ESCR (ENVIRONMENTAL STRESS CRACK RESISTENCE)
Resistenza alla rottura da stress ambientale è la capacità di un polimero di resistere alla rottura superficiale sotto carico
di una soluzione di tensioattivo. I valori sono espressi in ore (necessarie alla rottura del 50% dei provini secondo ASTM
D1693).
KISS-OFF
Zone di un manufatto rotazionale dove le due pareti opposte si avvicinano al punto da saldarsi (almeno parzialmente). Il kiss-off può essere passante e forma una specie di “tubo” che attraversa il manufatto; in tal caso nella terminologia corrente viene definito KISS-THROUGH. INDICE DI FLUIDITÀ (”melt-flow index”)
E’ la quantità espressa in grammi di polimero che fuoriesce in 10 minuti da un dato foro calibrato, quando soggetto a certe condizioni (di solito per il P.E. 190°C con 2,16 kg di peso applicato, secondo ASTM D1238).
E’ l’indice del peso molecolare medio: più alto è l’indice di fluidità, più corte sono le molecole di un dato polimero. MELT-INDEX o MELT FLOW INDEX vedi INDICE DI FLUIDITA’ POLIETILENE LINEARE LLDPE
Dal punto di vista chimico è lineare ogni polietilene con struttura che si sviluppa longitudinalmente (cioè senza ramifica-zioni importanti). Nel linguaggio corrente, si definisce polietilene lineare quello ottenuto da comonomero che garantisce ramificazioni molto corte (di quantità e tipologia controllabili). POLIETILENE RETICOLATO
E’ ottenuto per reticolazione (cfr.) del polietilene lineare reticolabile che avviene durante il processo dello stampaggio. Il
ciclo di stampaggio del PE reticolabile è di solito più lento a causa della più bassa temperatura di cottura (imposta dalle
esigenze della reazione di reticolazione).
PUNTI SINGOLARI
Sono i punti di un manufatto rotazionale nei quali lo spessore può differire, anche sensibilmente, dallo spessore medio del manufatto: flange, kiss-off, inserti metallici, sommità di nervature, spigoli vivi, zone di accesso difficile per la pol-vere, etc. Nei punti singolari non si applicano le tolleranze standard. RETICOLAZIONE (”cross linking”)
Reazione chimica che crea un legame tra due diverse catene molecolari ad opera di un perossido. Quando la retico-lazione è completa, tutte le molecole sono collegate in una unica “macromolecola”. Il test di reticolazione consiste nel disciogliere (con solventi molto aggressivi in condizioni estreme) le molecole rimaste non collegate; quelle collegate tra loro dalla reticolazione non vanno in soluzione e rimangono alla fine del test in forma di gel. Il rapporto tra il peso del gel e il peso del provino originario esprime il grado di reticolazione. SFIATO
Tubo inserito nello stampo che mette in comunicazione l’interno dello stampo con l’atmosfera esterna, consente di evitare (o quanto meno ridurre) la sovrappressione (in fase di cottura) e/o la depressione (fase di raffreddamento); ov-viamente il prodotto finito riprodurrà anche l’impronta dello sfiato. SOFFIATURA
Bolle create nello spessore del polietilene dall’aria soffiata nel materiale (fuso) proveniente dall’esterno (in zone di flange, inserti, sfiati, etc.) oppure da porosità dello stampo. Le prime sono causate dalla depressione di inizio raffredda-mento e si eliminano rimuovendo lo spiraglio di entrata e/o la causa della depressione (sfiato insufficiente). Le seconde si eliminano rimuovendo la porosità dello stampo oppure aumentando la sezione dello sfiato. SOTTOSQUADRA
Zona che interferisce con le flange dello stampo in fase di estrazione. Di solito sono protuberanze verso l’interno e verso l’esterno della figura. Manufatti con sottosquadra fino all’1% sono di solito estraibili con facilità (grazie al ritiro). SPANCIAMENTO (”warpage”)
Deformazione prodotta in un manufatto rotazionale dalle tensioni causate dalle non uniformità di raffreddamento (e
conseguente ritiro). Si evidenziano soprattutto nelle grandi superfici piane, che si raccomanda perciò di “spezzare” (con
nervature) o di evitare (con raggi di curvatura)
TEXTURE = FINITURA SUPERFICIALE
E’ la tramatura superficiale del pezzo (es. finta-pelle, buccia d’arancia, etc.) normalmente si riferisce alla configurazione
e/o alla profondità dei rilievi superficiali
ZONE DI PONTE (”bridging”)
Zone di scarso riempimento provocato dal contatto delle particelle aderenti ad una parete con quelli aderenti alla parete opposta. Il “ponte” si può creare in corrispondenza di passaggi troppo stretti e può essere causato da un disegno non ap-propriato dello stampo o da rotazioni sbagliate o, infine, da polvere di polimero non sufficientemente scorrevole.
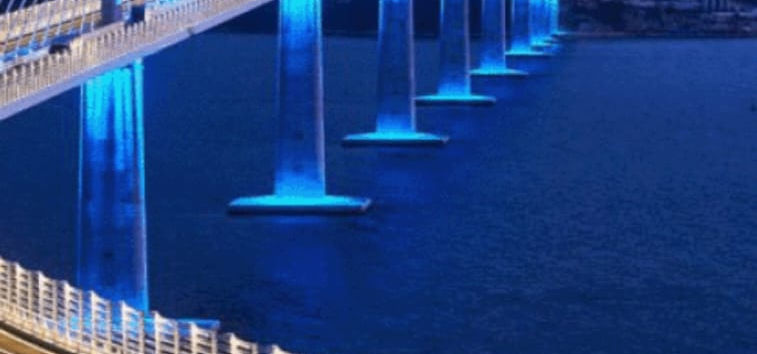
IN VETRINA, PONTI GALLEGGIANTI STARTUP
Scatti da incorniciare
Floating Bridge Global Sul link
https://andreasalvatorebuf9.wixsite.com/floatingbridgeglobal
Diventa Socio a partire da 20€
Info: andreasalvatorebuffa@gmail.com
Domicilio Elettronico Certificato PEC: buffa.andrea.salvatore@mypec.eu
Le condizioni necessarie per accedere ai Fondi Europei sono due:
Il capitale di minimo 50 mila euro.
Ricerca innovativa tecnologica, nuovo know-how Diventa Socio, Ponti Galleggianti
https://andreabuffapetrosino7.wordpress.com/2023/11/07/partnership-costruzione-di-ponti-con-andrea-salvatore-buffa/
Si tratta di creare dal Brevetto una azienda leader e innovativa.
Per la costruzione di Ponti Galleggianti.
Conosco molto bene la tecnologia e ho il know-how per la produzione con bassi investimenti.
Produzione che consiste nel piegare di un certo raggio le lamiere d’acciaio attraverso 3 rulli in metallo di 6 metri di lunghezza.
Saldare le parti con software opportuno e portare il cantiere in loco.
Il montaggio avviene in mare con un metodo semplice da far supporre il montaggio di 3 km di un ponte in un paio di mesi al massimo ma con moduli già esistenti.
I moduli vengono costruiti in terra ferma e poi varati in mare dove avviene il montaggio.
Qui le prove che ho richiesto Domanda di Brevetto per
Ponte Galleggiante in data 03/11/2023
Deposito Numero:
Ponte Galleggiante Deposito Brevetto 03/11/2023 – Andrea Salvatore Buffa
Sono un Progettista Industriale e uno Yacht Designer,
laureato all’ISIA di Roma e ho anche un Master in Yacht Design.
Qui il mio portfolio e il Curriculum
:
Le condizioni necessarie per accedere ai Fondi Europei sono due:
Il capitale di minimo 50 mila euro.
L’immagine di sopra è la prima pagina del Documento di prova di deposito per Brevetto.
Qui la descrizione del Progetto finora pubblicato con le indicazioni su come partecipare:
Un ponte Galleggiante Startup – Andrea Salvatore Buffa
Qualche girno fa,
The Bridgehunters Chronicles l’ha nominato “Ponte dell’anno” –
07/11/2023
Prego in nome di DIO di divulgare e spero che ne farà parte di questa avanguardia,
_
LA CONCORRENZA
Ci si riferisce a WeBuild Group
https://it.m.wikipedia.org/wiki/Webuild
In 117 anni di storia Webuild ha dato il suo contributo allo sviluppo dell’ingegneria civile realizzando 285 tra ponti e viadotti in tutto il mondo, per una lunghezza totale di 946 chilometri.
https://www.webuildgroup.com/it/ponte-sullo-stretto/
CONTATTACI
andreasalvatorebuffa@gmail.com
OPPORTUNITÀ DI CARRIERA
In quanto Laboratorio sulle infrastrutture in continua crescita, stiamo cercando di espandere il nostro team. Di seguito è riportato un elenco di posizioni aperte. Contattaci per qualsiasi domanda sul processo di candidatura o invia il tuo CV e lettera di presentazione per candidarti.
INGEGNE, ASSISTENTE DI RICERCA
Il suo Compito sarà di redigere i calcoli del progetto Ponti Galleggianti
DIRETTORE AMMINISTRATIVO
Dovrà occuparsi di tenere in ordine le economie di Global Floating Bridges
INGEGNERE CERCASI
Dovrà stendere il piano costruttivo redigere e firmare i calcoli necessari all'approvazione ufficiale
Il sottoscritto Andrea Salvatore Buffa, nato a Palermo il 2 marzo del 1973, acconsente al trattamento dei dati contenuti in questo sito web e alla libera circolazione di tali dati secondo il Regolamento (UE) 2016/679 del Parlamento e del Consiglio europeo.
LA DIVULGAZIONE È CONSENTITA ESCLUSIVAMENTE CITANDO IL NOME DEL SUDDETTO TITOLARE DELL’OPERA ANDREA SALVATORE BUFFA SECONDO L’ART. 10 CONVENZIONE DI BERNA;
andreasalvatorebuffa@gmail.com
CONTATTACI
andreasalvatorebuffa@gmail.com
©2023 di Floating Bridge Global. Creato con Wix.com